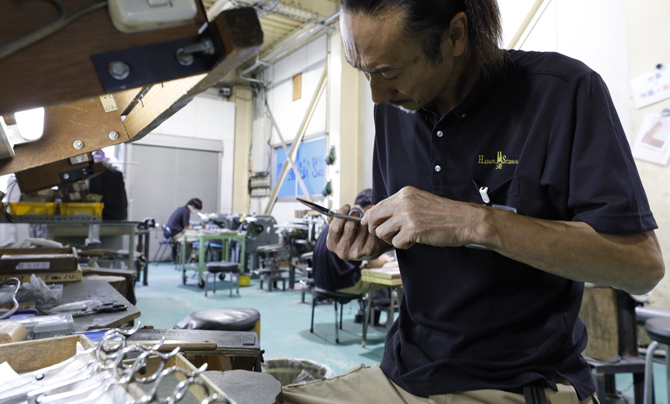
I hate half-baked things. Once a decision is made, aim for the top.
Mr. Hayashi started his new scissors making job even though he had never thought about them before. He thought about quitting his job only once as he was still young. “I thought this job wasn’t right for me, so I told my father that I wanted to quit. He just said, 'Ok, do as you like'. So I somehow contrarily decided to continue the job… I have a bit of a perverse character. I will want to do something after I’ve been told not to do it. My father could read me like a book.” Mr. Hayashi is a competitive character at heart, so he decided to be No.1 and restarted. “It’s easy after setting a goal. There are only two things for success, 'Do' or ‘Not do'.” Mr. Hayashi says simply, “I have no choice but to do it.” The production of scissors, however, involves numerous processes and it is only possible to learn it through a hands approach. It takes many years to become competent. Mr. Hayashi wanted to improve his skills quickly, so he asked his colleagues to teach him the process they were in charge of after work. Still he was not satisfied so he acquired more skills through self-study. He went independent after he knew how to make and repair scissors. “I went independent, but I did not have any customers as I kept to refining my manufacturing technique only. Of course, I had no sales experience, so I asked friends to teach me about sales. Then it was visiting numerous beauty salons and business started with sharpening scissors."
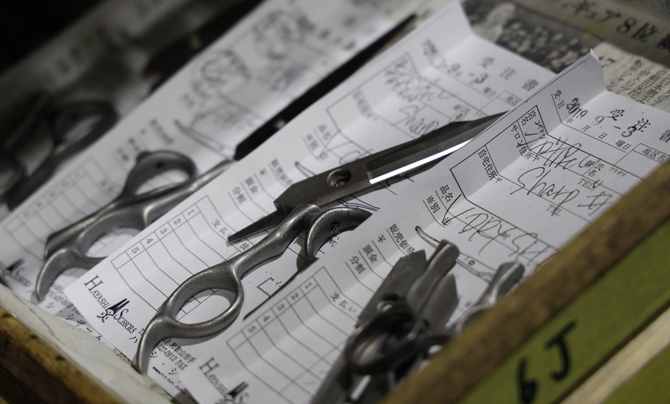
Providing an ideal custom-made scissors to each hairdresser, rare in the hairdressing industry.
“I think the hairdressers were also nervous at first. They were entrusting their important scissors to a young stranger to sharpen.” Mr. Hayashi promotes his wares not only in his local Kansai Region of West Japan, in places such as Wakayama and Osaka, but also in the Kanto Region of Eastern Japan. His way of promotion developed step by step and took time, but it works well. This is because he could hear from each hairdresser about what are ideal shapes and opinions about handing the scissors which he had sharpened. “I made custom scissors which were tailored to the shape and size of each person's hand.” Until then, it was common for scissors to be chosen and ordered from a catalog. But Mr. Hayashi can pick up even the smallest requirements from hairdressers about length, balance, and weight then finish the scissors all the while making adjustments along the way. The hairdressers aren't made to adapt to existing scissors anymore. Although it takes time, the scissors in the hands of the hairdressers are the ideal scissors to fit their hands. They are comfortable to use and retain excellent sharpness. Impressed hairdressers became repeat customers. “As a company that manufactures and sells by itself, I think we probably have the widest variety of scissors available in this industry. Every hairdresser has different preferences and cutting methods. "I want to be able to say, 'Yes, of course' when asked, ’Do you have this?' In the future too."

Making the strongest effort in the world, to be the best in the world.
“In recent years, the evolution of car safety has been remarkable. When I was little, I could never have expected that a car would be able to stop automatically. While car technology is already in a dream-like era, scissors haven't evolved significantly. That's why I have a passion to see a dream with scissors too." ‘HYS-MAX67’ are scissors made with such a strong passion. “Scissors must be sharpened regularly. So, maintenance-free would be dream scissors. It was a difficult but interesting challenge. A hard metal with a high wear resistance lasts a long time. However, they don't have a toughness or persistence as a material. Furthermore, a material with a high hardness has the disadvantage that it can be easily broken during the production process. “We have succeeded in developing a blade technology that uses a tough base material welded to a high-hardness powdered coated high-speed steel." Mr. Hayashi also developed a machine for in-house durability testing. Even if a hairdresser uses the scissors on 20 people a day, 20 days a month, the results showed that there is no problem for 3 years. So why develop an inspection machine? Mr. Hayashi answered, “My current goal is to be the best in the world. We have to make the strongest effort in the world to reach that goal. So all I do is all I need to do. That is all I need.” At the end we asked Mr. Hayashi about his future dream and he said it is to make a large-scale factory. “I am here now because I was given a job when I was in my 20's even though I had a handicap with my leg. It’s my dream to make a huge factory where people with handicaps like me can work comfortably. I think I can return the favour to this country by doing so.” As someone who has accomplished every goal he has set, we believe that Mr. Hayashi will surely make this dream come true in the near future.